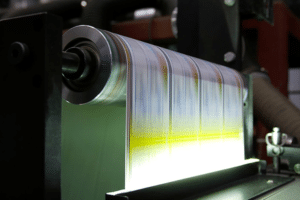
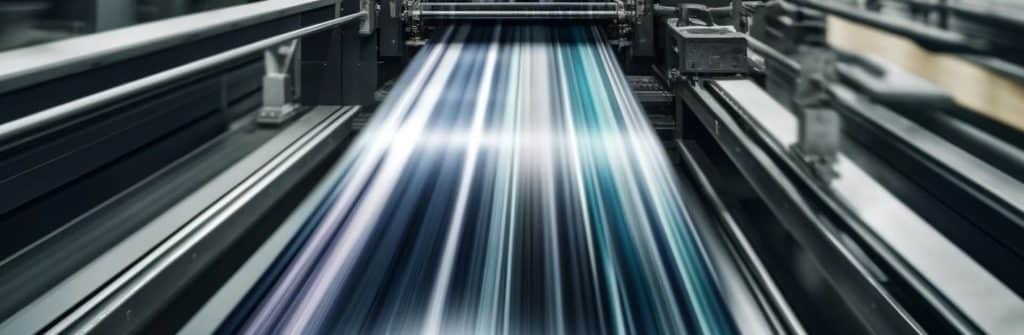
Material Samples & Specification
Rapid Quotation Turnaround
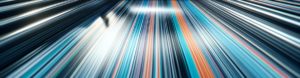
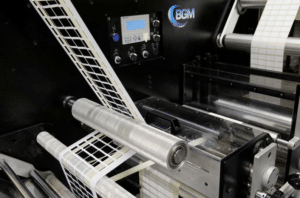
Our Process
At Sprite we put our trade customers and their clients at the heart of our thinking.
We are openminded and flexible in our workings to ensure that we deliver the most suitable product and service. Our diverse production capabilities enable us to produce a broad range of products.
This diversity often acts as a springboard for innovation enabling us to tailor solutions for our clients.
To arrive at a solution, we collaborate with you as well as our trusted suppliers to identify problems and the materials that might improve performance. Depending on the nature of the problem and size of the project, we might produce trials before launching into production.
To discuss an application or enquiry please use this form:
Our Relationships
At the very core of Sprite is our continued strength in maintaining lasting relationships with our suppliers and customers. We have often improvised new solutions, in conjunction with the invaluable support of our suppliers. In these cases, the benefits to the relationship between our customers and their client have been enormous and long standing.
Our Solutions
Industrial Label Application
Retail Label Solution
The retail end user had a cardboard booklet/tag attached by string to the bridge of their sunglasses. It was felt that this deterred customers from trying on the glasses, and was a barrier to sales. An additional problem was that some of the tags were removed by customers wishing to try the glasses. This was a serious issue as European law meant that the tag had to be in place. Working with our trade partner, Sprite proposed the use of a specially shaped booklet label, to be affixed to the side frame of the glasses. This was tested and found not to interfere with the trying on of the sunglasses. In addition, a pricing sticker was applied to the reverse of the new tag, meaning that the new product was able to fulfil a second function.
Company Process
Our client was asked to supply reinforced loop tags on A4 sheets for laser printing, following trials. Initial trials at one test site went well, but not so well at a second site. The end user was a large group of companies, and we found that each had different hardware. We liaised with the material manufacture to seek out a manufacture of printers that would guarantee their product. This led to the identification of a printer model and material that were guaranteed to be compatible. The solution proved to be robust and has been in place for several years.
Window Sticker Application
The label user had been able to write onto the reverse of their window stickers. However, due to much greater volumes, it became necessary to laser print the reverse of the window stickers. Unfortunately, there was no material construction in the market that allowed material suitable to act as a window sticker to also enable printing by laser. Sprite conducted various trials on combinations of materials designed to overcome the problem, and were able to demonstrate a solution that met the customer’s requirements.
Industrial Label Application
The end user company wanted to combine their marketing label, picking label and despatch label into one. In collaboration with our trade partner, the solution involved new software for the warehouse, thermal transfer print and a novel label construction. The marketing label was first printed, and then in-line, a second, removeable, label layer was applied over part of the label surface. This second layer accepted the picking and routing information from the thermal transfer printer. Once picked and delivered, the upper label layer was discarded, leaving the marketing label in place. This solution saved the user several hundred thousand pounds, by reducing the cost of labels, cost of application and through efficiencies in warehousing.
Retail Label Application
The retail end user had a cardboard booklet/tag attached by string to the bridge of their sunglasses. It was felt that this deterred customers from trying on the glasses, and was a barrier to sales. An additional problem was that some of the tags were removed by customers wishing to try the glasses. This was a serious issue as European law meant that the tag had to be in place. Working with our trade partner, Sprite proposed the use of a specially shaped booklet label, to be affixed to the side frame of the glasses. This was tested and found not to interfere with the trying on of the sunglasses. In addition, a pricing sticker was applied to the reverse of the new tag, meaning that the new product was able to fulfil a second function.
Company Processes
Our client was asked to supply reinforced loop tags on A4 sheets for laser printing, following trials. Initial trials at one test site went well, but not so well at a second site. The end user was a large group of companies, and we found that each had different hardware. We liaised with the material manufacture to seek out a manufacture of printers that would guarantee their product. This led to the identification of a printer model and material that were guaranteed to be compatible. The solution proved to be robust and has been in place for several years.
Window Sticker Application
The label user had been able to write onto the reverse of their window stickers. However, due to much greater volumes, it became necessary to laser print the reverse of the window stickers. Unfortunately, there was no material construction in the market that allowed material suitable to act as a window sticker to also enable printing by laser. Sprite conducted various trials on combinations of materials designed to overcome the problem, and were able to demonstrate a solution that met the customer’s requirements.